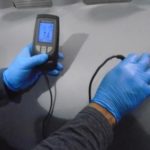
Tristar Coatings is pleased to offer a wide variety coating testing services. Our state of the art laboratory coupled with our experienced in-house chemists Tristar can provide quick and accurate results for your products.
Cup gun, siphon feed, air-assisted airless
Tristar can set the rheological properties (viscosity at a given sheer rate) of a paint to suit your particular application. A very thick paint can be challenging to spray and thinning would reduce opacity. Likewise a very thin paint would take many coats to get good opacity when attempting to brush or roll onto a surface. Finished products can be tested using customer specific application methods to ensure the adoption of Tristar products is a seamless as possible. An assessment can be done by our trained technical staff to help maximize efficiency
Walk-in spray booth for larger pieces
Refinish automotive applications or other type of industrial applications (metal doors/windows/parts) can be sprayed in the spray booth ensuring no dust buildup on a freshly painted surface before drying. Samples can be sprayed here to show potential customers or for special applications as required
Colourmatching can be done by eye or by computer analysis. Any colour source can be selected, not just from a colour chip. Almost any flat surface can be scanned and a paint sample prepared to closely match as required. The colour of a surface can look different depending on the light source, so it is important when requesting a colour match to include the typical source of light will be coming from, such as flourescent or incadescent lighting or natural light from the sun.
The gloss of a surface can be matched to a surface, and when matched properly along with colour a touch-up can blend in perfectly. As paint ages in the sun, the gloss can drop. A high gloss paint (>90) that requires a touch-up could require a gloss closer to a satin coat around 50-65 if it has aged for a significant length of time.
Pencil Hardness
This gives the relative hardness of a coated surface by trying to scratch a painted surface with an increasingly hard pencil. The harder the pencil required to cut into a paint coating, the harder the coated surface which can show up in reduced scratching or gauging.
Sward Rocker Hardness
Another method for determining film hardness, a circular Sward Rocker is rocked back and forth until it no longer rocks past a certain point. The higher the number obtained, the harder the painted surface.
Pull Off Testing
This test involves using a 2-part epoxy to glue a metal piece onto a painted surface. Once fully cured, a pneumatic pump is then used to try to pry off the metal piece. The amount of pressure required shows how good the adhesion is. This can be further complicated when the coated surface is both primed and top coated and possibly even clear coated. Analysis can also include what exactly failed – was the failure between the primer and topcoat? This could help protect the surface if the topcoat gets pulled off but leaves the anti-corrosive primer. Did the failure go straight down to the substrate? This could indicate poor surface preparation prior to application of the primer. If only a topcoat is applied, this could show the need for a primer or a modified coating for increased adhesion.
Cross Hatch
This is a real-world test that shows what happens to the adhesion of paint to a surface after the surface gets scratched right down to the substrate. Four parallel lines are cut into a painted surface in two directions, 90° to each other. A certified tape is then applied and allowed to rest prior to quickly pulling off. The amount of paint removed in the tiny squares made from the cut lines shows the relative adhesion.
Conical Bender
A test completed on a metal panel that checks adhesion of a coating on a metal panel. This version bends a panel over a conical piece of steel at an increasing diameter, the smaller the diameter the more challenging the test. Cracking and or delamination is a failure for this test at a given diameter.
Cylindrical Bender
A test for adhesion completed on a metal panel, this bends a coated panel over a cylindrical piece of steel. The diameter can be decreased down to as small as 2mm and as large as 32 mm. Smaller diameters are significantly harder to pass than larger diameters. Cracking and or delamination is a failure for this test at a given diameter.
This is a deformation test where a known weight is dropped from a known height onto a metal panel. This can be done from the front where the paint is pushed in, or from the rear of the painted surface where the paint is pushed out. Failures are identified by cracking or delamination in the deformation. Higher drops or weights are more challenging to pass. When comparing two samples, the same panel preparation and film build must be used as a comparison.
Tristar Coatings offers a wide range of fluid resistance testing services.
Following industry standards we can provided timely and accurate results.
ASTM D471 Ref Fuel B
BAMS 564-003 Type IV Phosphate Ester Base Hydraulic Fluid
Hydraulic Fluid, Petroleum Base; Aircraft Missile and Ordinance.
Lubricating Oil, Aircraft Turbine Engine, Synthetic Base
MIL-PRF-87257 Hydraulic Fluid, fire resistant, low temp, synthetic, hydrocarbon-based.
Fluid resistance is a challenging test where coated panels are allowed to cure fully, then submerged into a fluid for a specific amount of time. Once the time has elapsed, the panel is wiped and tested for adhesion. A passing fluids test gives the same good adhesion from a panel that did not undergo submersion in fluids. These are typically done in aerospace applications, but could have valuable information on a shop floor where other fluids like antifreeze or oil could be present and could negatively impact performance
Salt Spray (ASTM B117) and Prohesion (G85) available
These two tests arr done on metal substrates and simulates corrosion in exterior aplications. A panel is coated as normal and allowed to fully cure. These panels are then cut in an X pattern on the front through the coating, right down to the substrate. Panels are put into an environmentally controlled chamber filled with a salt fog of known concentration. The number of hours without corrosion is then measured, and the level of corrosion at a given # of hours can give an idea on how well a coating will perform in the field. Ideally a comparison is done with a known standard. Certain paint chemistries are better able to resist corrosion, alkyds typically last only a few hundred hours with anti-corrosive pigments while epoxies/urethanes can easily last longer than 1,000 hours. When requesting this type of testing be sure to indicate standard salt spray or prohesion.
UV testing puts a cured panel under UV a cycle of UV radiation and deionized water. This simulates what happens to a painted surface when left out in the sun. Refinish industrial applications on heavy equipment, commercial signs and architecural applications would benefit from this testing to see how the paint will fade over time. Typically industrial testing is over 1,000 hours depending on the paint chemistry involved.
Absolute Dry Film Thickness
This is a test that shows how much dried paint is on a coated surface. Too high of a film build can cause curing or adhesion problems and too low can either have poor opacity or could have ineffective anti-corrosive properties.
Surface Profile Gauge
This analyzes the surface of uncoated surface. A very high profile can be hard to coat with a smooth surface and the peaks could not have enough paint on it to properly protect the surface, leading to corrosion. Likewise too low of a profile could be hard to have good adhesion.
Multi-Layer Analysis
This is typically used on a painted surface that is coated in a primer, a topcoat and potentially more. Variations in colour aids in the identification of each layer, but a hole is cut into the painted surface at a 45° angle to the surface. With the angle known, the width of each layer can be used to calculate the thickness of each layer.
This can be used in many ways, from analysis of film build to analysis of failure points. A failure like a fisheye or a crator could be due to incorrect surface tension of the coating, or potentially due to contamination or escaping solvent vapour as the coating is drying. The source of the failure can potentially be identified and photographed under a microscope.
Coating comparison of dry coating as well as wet samples is available
CONTACT TRISTAR COATINGS FOR MORE INFORMATION ABOUT OUR TESTING SERVICES
* Please include specific testing requirements (ASTM test methods/aerospace specifications) in quote requests if required